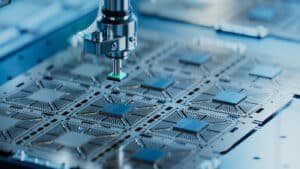
Pleated Filter Cartridge
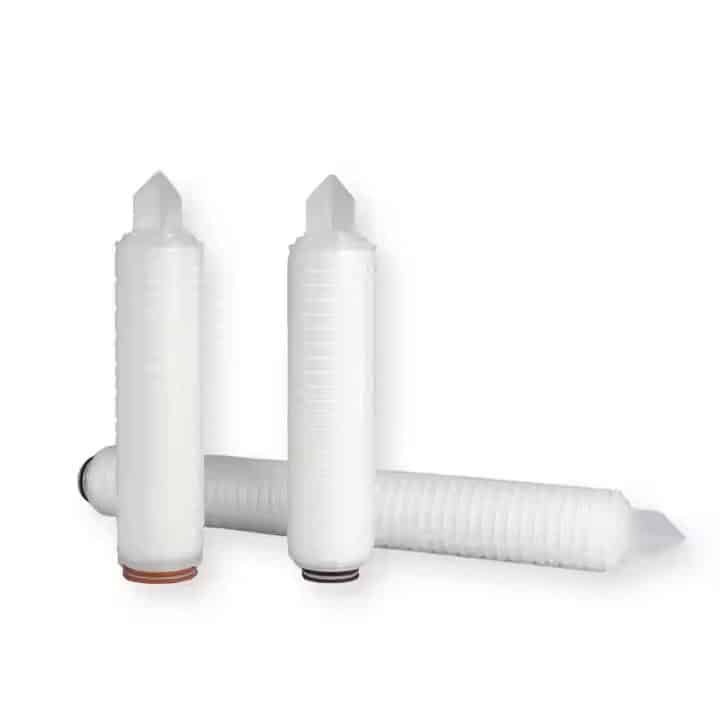
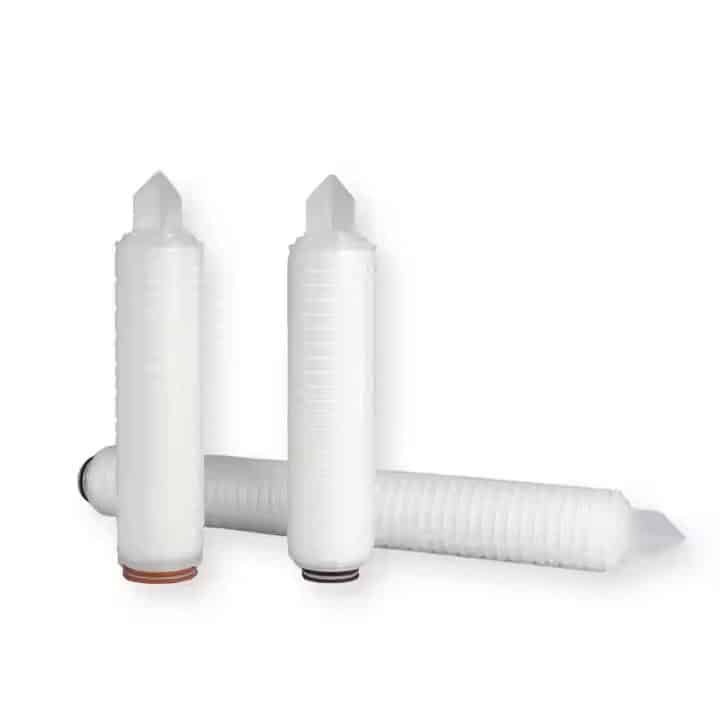
1. Introduction 🌟
Pleated filter cartridge represent an essential class of filtration solutions used across industrial, commercial, and municipal systems worldwide. Their design combines high surface area, robust structure, and precise micron retention capabilities, making them suitable for demanding applications ranging from water purification to pharmaceutical processing. This product category page aims to provide an exhaustive guide for overseas buyers—procurement specialists, engineers, distributors, and OEMs—detailing core functionalities, applications across industries, product variants (PP, Nylon, PES, PVDF, PTFE), selection criteria, maintenance practices, industry standards, advantages, and frequently asked questions.
2. Understanding Pleated Filter Cartridge
2.1 What Are Pleated Filter Cartridges?
Pleated filters consist of folded layers of micro- or ultrafiltration media. This pleating increases surface area (up to 10× compared to flat filters), allowing for higher flow rates and greater contaminant capture without high pressure drop. Constructed inside a cylindrical cage, the media is supported by perforated cores to prevent collapse under pressure. End caps and gaskets provide reliable sealing and system fit.
2.2 Comparison to Spun/Depth Filters
Unlike depth filters that capture particles throughout thick fiber layers, pleated filters rely on precise pore structures on the media surface. This enables ultra-fine filtration (as low as 0.01 μm), critical for bacteria, yeast, and colloid removal. Additionally, pleated cartridges tend to have lower operating costs over time and are easier to sanitize and re-use where applicable.
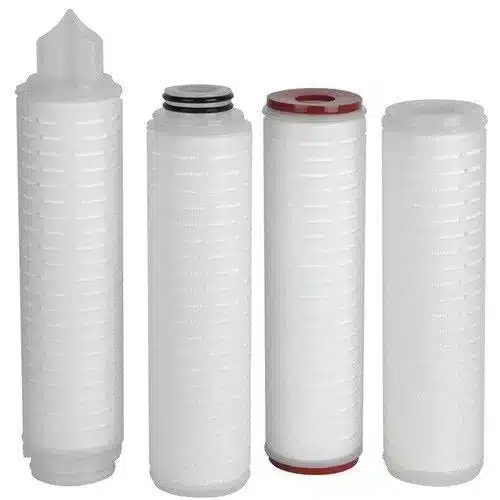
Types of Pleated Filter Cartridges
3. Applications of Pleated Filter Cartridges
Pleated filters serve across industries due to their adaptability, precision, and regulatory robustness.
3.1 Water Treatment & Purification
Hospitals, laboratories, beverage plants, and municipal water systems rely on pleated filters for pre-filtration before RO, UV, or distillation units. Depending on grades (0.2 μm–5 μm), filters can eliminate turbidity, bacteria, cysts, and suspended solids. PP and PES variants are common; PVDF/ PTFE are used when chemical resistance or sterilization is required.
3.2 Food & Beverage Industry
Used to clarify juices, wines, beers, syrups, and edible oils:
PES filters (0.45–1 μm) remove spoilage microorganisms.
PTFE hydrophobic filters (0.2 μm) ensure sterile filtration downstream.
Nylon filters withstand CIP cycles and hot-fill processes.
3.3 Pharmaceutical & Biotech
For critical sterile filtration steps and sample clarification, pleated filters in PES, PVDF, or PTFE materials remove bacteria, mycoplasma, aerosols, endotoxins, protecting bulk drug or biotech systems. Filters often undergo 100% integrity testing and are gamma-irradiated for aseptic operations.
3.4 Chemicals & Solvents
Pleated cartridges resist aggressive solvents, acids, and bases—especially PVDF/PTFE. Applications include fine chemical production, electronic chemicals purity, solvent recovery, and specialty coatings—requiring micron-level filtration while preserving chemical inertness.
3.5 Electronics & Semiconductor Industry
Critical contamination control in wafer fabrication demands <0.2 μm filtering. PVDF and PES offer low extractables and compatibility with ultrapure water and photoresist solvents, making pleated filters indispensable in fabs.
3.6 Oil & Gas, Petrochemical
In hydraulic units, fuel systems, and gas processing plants, pleated cartridges remove solids, slurries, and water emulsions. Nylon (hydrophobic) or PVDF tolerate elevated temperatures and corrosive fluids. PTFE filters play a role in protective venting.
3.7 Clean Room & Laboratory Use
Laboratories, hospitals, research institutes, and cosmetic production rely on sterile or bacterial‐retentive filters for solutions, air intake, and HVAC systems. Pleated filters with HEPA/PES media meet ISO Class 5–8 clean room standards.
4.Benefits That Set Pleated Cartridges Apart
High Filtration Surface Area: Pleats unlock 10–20x area vs cylindrical depth cartridges
Low Operational Cost: Longer life reduces labor and downtime
Consistent Filtration Efficiency: Better quality output and downstream protection
Versatility in Media & Gasket: Choose for varied industries
Easy Retrofit & Scale-Up: DOE 10–40″ standardization across systems
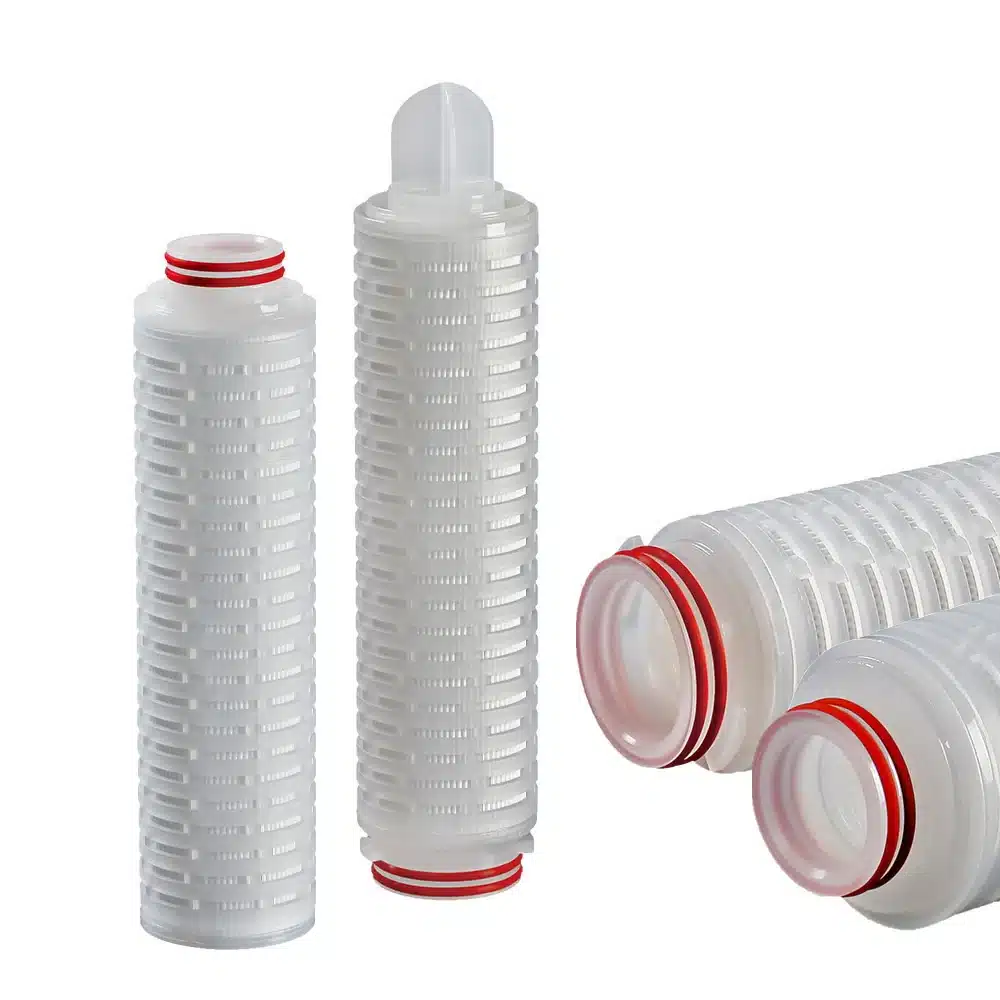
5. Types of Pleated Filter Cartridges
Here we break down the five major media types and their key attributes:
5.1 Polypropylene (PP)
Micron range: 0.45–100 μm
Best for: Sediment removal, chemical compatibility with aggressive pH
Pros: FDA-grade, low cost, broad media availability
Limitations: Temperaturehold: 80–90°C; weaker stiffness
5.2 Nylon
Micron range: 0.2–10 μm
Best for: Clarity polishing, fine particle retention
Pros: Large surface area, re-wettability, low protein adsorption
Limitations: Limited heat tolerance (up to ~90°C); acid vulnerability
5.3 Polyethersulfone (PES)
Micron Range: 0.05–5 μm
Best for: Sterile and bacterial-retention applications
Pros: Broad chemical compatibility, heat-resistant (up to ~120°C), low extractables
Limitations: Pricier than PP/Nylon
5.4 Polyvinylidene Fluoride (PVDF)
Micron range: 0.05–1 μm
Best for: Chemical & solvent resistance, wear durability
Pros: High-temperature tolerance (~150°C), strong mechanical resistance
Limitations: Higher cost, sensitive to high-heat sterilization if not supported
5.5 Polytetrafluoroethylene (PTFE)
Micron range: 0.1–1 μm
Best for: Sterile, hot chemical, oil-based, hydrophobic applications
Pros: Excellent chemical inertness, autoclave-safe (up to 150°C), low CHG/VOC
Limitations: Highest cost; requires rigid support core
6. Product Selection & Specification
6.1 Micron Rating & Retention Goal
Select based on target particles:
0.1–0.45 μm for bacterial removal
1–5 μm for industrial clarity
10–100 μm for containment and coarse filtration
6.2 Media Durability
Temperature: PP < Nylon < PES < PVDF < PTFE
pH & Solvents: PTFE & PVDF handle the most aggressive chemistries
6.3 Flow Rate & Pressure Drop
Balance flow demand vs cartridge area. For example, 10″ DOE pleated filters: 25–70 GPM depending on media type.
6.4 Regulatory Compliance
PP & Nylon: FDA CFR-177
PES, PVDF & PTFE: More suitable for USP Class VI, ISO 10993, 3-A food standard compliance
6.5 Housing Compatibility
Ensure housing materials (SS304, SS316L, PP) and gasket types (EPDM, silicone, FKM) match fluid, temperature, and foaming behavior.
7. Maintenance & Replacement Best Practices
7.1 Differential Pressure Monitoring
Replace cartridges when ΔP reaches 25–35 PSI (1.7–2.4 bar) over clean-state baseline or at scheduled intervals.
7.2 Cartridge Life & Dirt Load
Melt-blown/PP and Nylon typically replaced every 3–6 months; PES/PVDF/PTFE may last 6–12 months depending on fluid load.
7.3 Cleaning, Sanitization, Disposal
Heat sanitize PES/PVDF (up to 120–150°C) or chemical clean based on material rating. Proper disposal in compliance with local regulations for medicinal, solvent, or hazardous fluid residue.
8. Standards & Regulatory Compliance
8.1 FDA Food Contact
Materials such as PP, PES, PVDF certified under CFR Title 21, ensuring safety in beverage, dairy, & food contact.
8.2 USP & ISO
Consider filters with USP Class VI and ISO 10993 for medical, biotech, and pharmaceutical readiness.
8.3 Industrial Standards
3-A sanitation specification for dairy/food industry
NSF/ANSI 42 & 53 for water reduction claims
CE & RoHS for international regulatory markets
9. Frequently Asked Questions (FAQ)
Q1. What micron rating should I use for microbial removal?
Use <0.45 μm Nylon, PES, PVDF, or PTFE to reliably remove bacteria and some viruses.
Q2. How often should cartridges be replaced?
Replace at ΔP threshold or schedule (e.g., every 3–12 months), depending on fluid quality.
Q3. Can we sanitize cartridges in place?
Yes. PES/PVDF/PTFE allow SIP at 120–150°C; PP/Nylon require lower heat or chemical CIP.
Q4. How do materials differ for chemical resistance?
PTFE & PVDF handle strong acids, solvents, and organics. PES resists moderate solvents. PP/Nylon suited for water and mild acids/bases.
Q5. What’s the difference between disposable vs. reusable cartridges?
Disposable (diatomaceous earth, re-washable) vs. pleated single-use: Pleated offer easier handling and predictable performance but should be disposed.
Q6. Do pleated cartridges support ultrafiltration?
Not typically; for true ultrafiltration you need membranes. But 0.05–0.1 μm PVDF/PTFE may approach that level for colloids.
10. Conclusion
Pleated filter cartridges are cornerstone technology across industries due to their adaptability, robust performance, and regulatory compliance. By understanding material strengths—PP, Nylon, PES, PVDF, PTFE—your team can expertly match cartridge to application. Their high flow rates, dirt capacity, long lifetime, and compliance features make them invaluable.
For technical datasheets, product comparisons, or customized filtration packaging, our specialists are ready to assist.